Как пандемия коронавируса изменит автомобилестроение
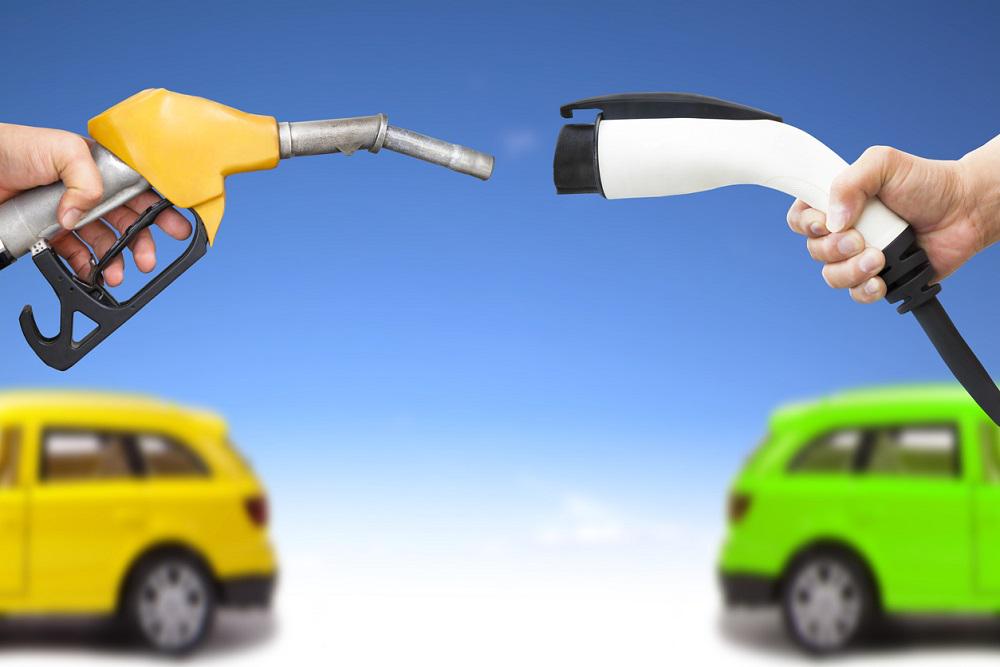
Чем нынешний кризис отличается от предыдущих экономических кризисов?
Владимир Щербаков: Может, звучит цинично, но коронавирус принес не только ощутимый ущерб, но и некоторые новые возможности, привел к решению ряда болезненных проблем, за решение которых производственники безуспешно бились годами. Главный плюс для экономики нашей страны от коронавируса в том, что наконец-то начали снижать процентную ставку, распечатали кубышки для увеличения накоплений.
Каждый предыдущий кризис, начиная с 1998 года и заканчивая 2015-м, проходил в том же технологическом укладе, в традиционной технологии, пространстве, рынке. Было понятно, что ничего радикально не меняется. И мы знали, что надо перетерпеть, сжать зубы, несмотря ни на что, даже на отсутствие зарплаты, - работать, хорошо подготовиться и очень быстро занять освободившиеся от ослабленных игроков ниши. Абсолютно ясная цель - не только удержать, но обязательно увеличить свою долю на рынке.
Сегодня и выход из кризиса радикально другой. И мир, в который мы выходим, тоже. Потому что пандемия наложилась на переход к новому технологическому укладу. Да, кризис - это всегда и возможности. Но какие новые возможности открывает мир после пандемии - пока не очень видно, чувствуешь себя "ежиком в тумане". Какие материалы и технологии станут базовыми для автопрома нового уклада, пока не понятно.
Что вы подразумеваете под новым технологическим укладом?
Владимир Щербаков: Например, кузова и двигатели, два главных компонента автомобиля. "Металлическая" жизнь кузова достигла преклонного возраста. На смену все увереннее приходят композиты, угле- или кремнепластики, химволокна и новые технологии формования. Уже сейчас в современных моделях пластики занимают от 30 до 50% веса кузова и свыше 20% его поверхности. В конструкции кузова все чаще применяется жесткий силовой каркас, защищающий жизненное пространство, и наружные заменяемые навесные детали. Помимо повышения безопасности, облегчения ремонта это позволяет легко менять навесные детали, быстро обновлять цветовую гамму и внешний вид автомобиля.
Фундаментальных препятствий для дальнейшего развития и ускорения этих процессов не существует. Все сводится к вопросам стоимости, следовательно, технологиям производства. На мой взгляд, Россия еще не опоздала на этот поезд, но пора бежать изо всех сил.
Мы угрожающе отстаем в производстве самих современных пластиков и химических волокон, в создании новых технологий их формования и окрашивания. Нам нужно ускоренно научиться создавать не только пластики с заданными параметрами упругости, текучести, ударопрочности и т.д., но и технологии производства компонентов и деталей из этих материалов. Никаких нерешаемых проблем на этом пути нет. Серьезные наработки в этой сфере были еще в начале 80-х годов. Первый в мире полностью из углепластика самолет был поднят СССР в воздух в 1982 году, в 1986-м технологии продвинули так, что самолет из композитов летал в стратосфере, а в конце 1988 г. в космос был запущен (и главное, возвращен точно на место) беспилотный "Буран". Все базовые технологии в России есть.
Это касается только кузовов?
Владимир Щербаков: Более сложная и неоднозначная ситуация с двигателем автомобиля. Остро стоит вопрос о выборе перспективного базового двигателя и топлива для него. Приходилось много раз высказываться о перспективах электрического и водородного двигателей в виде возможной базовой технологии будущего. У этих технологий есть масса противников и масса скептических отзывов. С переходом на электродвигатель связан радикальный пересмотр системы взаимодействия агрегатов и передачи управляющих воздействий. Электродвигатель позволяет убрать традиционную трансмиссию, мосты, карданы и т.д.: появляется возможность управления путем воздействия прямо на каждое колесо автомобиля.
Исчезают привычные и очень сложные в изготовлении коробка перемены передач, рулевые механизмы, гидравлические и пневматические тормозные системы, карданные приводы, мосты... Автомобиль приобретает новые эксплуатационные возможности. Отсутствие трансмиссии позволит сделать ровный пол и даст возможность создать различные компоновочные решения салона и его трансформацию. Очевидно, такие решения существенно уменьшат затраты не только на производство, но и на эксплуатацию.
Про электродвигатель сегодня многое, хотя и не все, понятно. Пока мы готовимся обсуждать эту тему в ходе подготовки очередной Концепции или Программы развития автопрома на перспективу, мировые лидеры ее для себя решили еще 10-15 лет назад. Они законодательно определили, что те, кто хочет работать на основных мировых авторынках, должны в течение 2020-2025 годов перейти на двигатели нового поколения, соответствующие резко возросшим требованиям по экологическим параметрам. Никто никого не заставляет переходить на электродвигатель. Просто автомобиль с традиционным двигателем внутреннего сгорания не допускается на основные рынки. Уже сейчас многие страны запрещают производство автомобилей с ДВС: одни к 2030 году, другие даже в 2025 году. Следующим шагом будет запрещение движения автомобилей с традиционными двигателями на своей территории.
Но на государственном уровне цель к 2025 году освоить серийное производство электромобилей не ставится. По крайней мере, в Концепции и Программе развития до 2025 года это не отмечено. Вместо серьезного обсуждения, что и как нужно сделать, чтобы занять достойное место в мировой гонке, все друг другу объясняют, почему электродвигатель для России не подходит. Одни считают, что батареи дорогие и слабые, при этом как-то забывают, что Россия - один из главных обладателей ресурсов лития и кадмия, и просто стыдно не создать лучшие технологии их переработки.
Другие бездоказательно утверждают, что электрический двигатель не годится для северной страны, хотя рядом пример Канады, Норвегии, Финляндии, Исландии и даже Аляски, по дорогам которых бегают уже десятки тысяч электромобилей.
А есть альтернатива?
Владимир Щербаков: Электродвигателям есть серьезная альтернатива и дополнение - водородные двигатели, в производстве которых еще не поздно стать лидером. Главное достоинство водородного топлива в том, что оно может применяться практически во всех видах двигателей - в ДВС, в газотурбинном, электрическом или гибридном двигателях как в роли топлива двигателя, так и топливного элемента электродвигателя. По эффективности бензин, дизтопливо или литиевая, кадмиевая батареи, как говорится, и рядом не стояли. Один грамм водорода дает в три раза больше энергии, чем один грамм бензина. Отсюда многократно выше стартовый крутящий момент, увеличенный запас хода и т.д. Кроме того, выброс СО2 и тяжелых металлов у таких двигателей равен нулю. Вместо серы и окислов азота они выбрасывают кислород и водяной пар, который снова превращается в воду.
Очевидно, что не все так сладко. Есть и серьезные трудности на этом пути. Хоть водород и получают гидролизом, он все же пока существенно дороже бензина. Для производства нужна пресная вода - а она постепенно становится дефицитным ресурсом. У России гигантское преимущество перед другими - запасы бесплатно тающего льда в Арктике огромны.

Главная проблема в том, что водород очень взрывоопасен, - для сжижения его сжимают в 850 раз, давление газа достигает 700 атмосфер, для поддержки жидкого состояния требуется температура ниже минус 250 градусов. Сжижать, транспортировать и хранить водород дорого и небезопасно. Это правда. Но кроме впечатляющих цифр сжатия и повышенной летучести он ничем не отличается от других видов газа, включая пропан, метан, кислород, азот, которые тоже в этих вопросах "не подарок", но ведь научились с ними работать.
Аргумент, что при эксплуатации любая авария автомобиля может стать смертельной, в значительной мере справедлив. Правда, для ситуации 12-15-летней давности. Сегодня в мире они находят неплохие решения. Например, уже есть технологии, благодаря которым водород вкачивается под давлением в специальные баки, изготовленные целиком из наносплавов, где находится в полутвердом невзрывоопасном состоянии. Это похоже на воду в поролоновой мочалке.
Образно выражаясь, водородный бак становится своеобразной электрической батареей, которая на два порядка эффективней литиевой. Представьте, как в ближайшем будущем на обычной заправке за 2-3 минуты заправляете в бак водород, который по расчетам можно опустить до современных 5 рублей за литр, и спокойно едете несколько тысяч километров. Это не пустые фантазии. Такие технологии и оборудование есть уже сейчас.
Создание водородного топлива и двигателей на его основе сегодня уже не фундаментальная проблема, а набор технологических вопросов.
Еще 60 лет назад СССР был впереди планеты всей по водородным технологиям. Как бывший председатель Госплана СССР, могу заверить, что и 30 лет назад СССР сохранял большой, измеряемый десятилетиями отрыв по достижениям в этой технологии.
Сейчас у многих вызывает удивление, когда я рассказываю, что еще в 1943 году во время блокады Ленинграда в городе на водороде работало около 600 автомобилей и около 50% воды перекачивали по трубопроводам с помощью двигателей на этом топливе. Опыта и знаний по этим вопросам в стране накоплено немало.
Но в мире эти технологии не сильно приветствуются...
Владимир Щербаков: В 2006-2008 годах целым рядом моделей с инновационными водородными двигателями практически одновременно, неожиданно даже для профессионалов мирового автопрома, выстрелили ВМW, GM, Toyota, Honda, Daimler, Audi... Это были пилотные, предсерийные экземпляры. Но уже в 2012 г. появились первые серийные модели. Toyota 3 года назад начала продажи первого в мире седана на водороде модели Mirai, а недавно объявила о начале продаж в 2020 году серийных моделей с водородными двигателями уже второго поколения. Этим летом Hyundai начал продавать первый в мире тяжелый грузовик на водородных топливных элементах. Сейчас по дорогам мира движутся уже десятки сотен тысяч автомобилей на водородном топливе, включая городские автобусы в Европе.
Если автомобили с двигателями внутреннего сгорания будут выдавливать, то куда?
Владимир Щербаков: Не думаю, что в металлолом. Автомобили и оборудование переместят, а скорее, дешево продадут в менее развитые и требовательные страны. Не хотелось бы, чтобы, как в 1990-2000 годах, все это старье скинули в Россию, мы просто обязаны выйти на мировые стандарты, конечно, с учетом особенностей климата, дорог, расстояний, потребностей в военной и специальной технике, но в любом случае не должны допустить превращения страны в "затерянный мир".
В качестве одной из мер целесообразно было бы поднять технические и экономические барьеры защиты нашего рынка для автомобилей прямого импорта. Действенная мера господдержки, которая сейчас остро нужна отечественному производителю, - сделать автомобиль прямого импорта неконкурентоспособным по цене с произведенным в России. Сейчас было бы своевременно провести такие меры, поскольку российский автопром способен удовлетворить практически все разнообразие вкусов отечественных потребителей. Но еще более необходимо напряженно работать над собственными технологиями и материалами.
Как пример развития технологий можно припомнить Tesla? Может ли эта компания задавать технологические тренды будущего для автомобилестроения?
Владимир Щербаков: По части идей создания производства на качественно новом уровне - практически полной цифровизации всего жизненного цикла автомобиля, формирования трендов развития нового технологического уклада, направлений радикального изменения облика промышленного производства - Tesla уже сейчас - это действительно очень круто.
Для получения автомобиля в нынешнем технологическом укладе должен работать огромный промышленный комплекс - нефтяная и газовая, рудная и угольная, металлургическая, металлообрабатывающая, электронная, электротехническая, химическая, нефтегазоперерабатывающая, легкая, текстильная и другая гигантская, в научно-инженерном и организационно-кадровом содержании очень сложная, трудоемкая и фондоемкая, географически, а часто и политически, разобщенная производственная цепочка.
Если удается из всех участников цепочки создать квалифицированный оркестр, в котором каждый точно исполняет свою партию, то в конце появится двигатель, кузов, 20 тысяч комплектующих изделий. Все они должны вовремя собраться в одной точке и преобразоваться в автомобиль. Кроме того, нужно произвести также бензины, масла, без которых машина не поедет. Например, в автомобиле BMW (а это в принципе вершина действующего уклада) около полутора тысяч трущихся деталей. Их надо изготовить, испытать, собрать, смазать... В Tesla Модель З (первое поколение нового технологического уклада) трущихся деталей всего 130-150. Очень много композитов, новых технологий формования на основе 3D-технологий, в производстве - сплошь электроника, робототехника...
Эффект от подобных инноваций в действительности колоссален. С точки зрения организации производства автомобиля это означает, что автопрому больше в таких масштабах не нужна прежняя металлургия и традиционная металлообработка, радикально меняются требования к продукции таких отраслей, как химия и нефтегазохимия, вместо традиционных методов формования пластмасс и металлов требуются аддитивные технологии. Резко сокращается потребность в объемах добычи руды, угля, нефти, газа, редкоземельных металлов, а также в транспорте. Для получения деталей нужных конфигураций и параметров больше будут не нужны длинные, сложные и дорогостоящие линии обработки. Детали точных параметров и расцветок можно будет экструзировать или печатать прямо в точке сборки или продажи, исключая дорогостоящую оснастку, упаковку, транспортировку.

Только для автопрома придется менять всю промышленность?
Владимир Щербаков: Автопром - локомотив для всего производственно-хозяйственного комплекса. Изменяя свои запросы, он требует адекватного изменения в поставляющих отраслях. Даже если не произойдет полной замены на электродвигатель и сохранится необходимость производства двигателей внутреннего сгорания, то действующая техническая база производства ДВС радикально изменится.
Например, линия механической обработки блока цилиндров на "КАМАЗе" - это цепочка очень сложного и дорогостоящего оборудования около 400 метров длиной и двух метров высотой. И это только одна линия. А еще есть литейный завод, который должен этот блок отлить из чугуна или алюминия. Теперь все это будет не нужно. Требуется одна установка, в которую загружаешь металлические гранулы и на выходе получаешь готовый блок двигателя. В перспективе, технологии разовьются и до печатания сразу готового двигателя. Этот процесс также стремительно пойдет и в других отраслях. Такие процессы радикально изменят не только предмет, но и направления инвестирования .
На каждый новый вызов должен быть подготовлен адекватный ответ. В противном случае рискуем инвестировать в отмирающие технологии, когда уже появились новые.
Традиционный двигатель внутреннего сгорания обречен?
Владимир Щербаков: Его перспективы становятся более сложными. У каждого технологического уклада есть свои сроки жизни. Думаю, традиционная схема ДВС завершает свой жизненный цикл. В легковом сегменте и легком коммерческом транспорте, как сказано, на мировом рынке уже идет активное замещение ДВС прежде всего на электромобили, а затем водородные технологии. В грузовом сегменте бензиновых двигателей немного. Традиционный дизель может в обозримой перспективе сохраниться для коммерческого транспорта, прежде всего дальнобойщиков - пока дешевле и надежней для них ничего нет. Следует иметь в виду, что при всем разнообразии видов транспорта около 70% грузов в мире перевозится автотранспортом. Замены ему в перевозках "от порога до порога" человечество пока не придумало. Да и создать инфраструктуру для другого топлива по всему земному шару так быстро не получится. Думаю, у ДВС на дизтопливе есть еще лет 15-20 впереди, при условии постоянного улучшения экологических, технических и экономических параметров.

Владимир Щербаков родился в 1949 году. Трудовую деятельность начал в 1969 году на строительстве Волжского автомобильного завода в Тольятти.
В 1988 году назначен министром СССР по труду и социальным вопросам. В 1990 году назначается сначала заместителем, а затем первым заместителем премьер-министра СССР - председателем Госплана СССР.
В 1994 году под руководством Владимира Щербакова была разработана Программа создания производства современных легковых автомобилей в Калининградской области и основана компания АВТОТОР - крупнейший автопроизводитель России.
Доктор экономических наук, профессор, в 2019 году стал лауреатом премии "Экономист года" за создание комплекса автопроизводств в Калининградской области.
- Ушаков: Спецпосланника Трампа Уиткоффа на этой неделе ждут в Кремле
- Ставший последним оплотом ВСУ на Курщине Горнальский монастырь освобожден
- Путин объявил о планах провести саммит с арабскими странами
- Российские военные освободили поселок Сухая Балка под Дзержинском в ДНР
- Швейцария ввела санкции против восьми российских СМИ
- Похороны папы Франциска состоятся 26 апреля